Reverse Logisticsl
Data-Driven Innovations in Waste Collection and Disposal
Data-driven efficiency.
Our algorithms use all relevant information about the waste types, pick-up locations, vehicles permissions and availability of waste receiver facilities.
Actionable insights.
Realtime and historic information about the full process. Follow the drivers and analyse their progress. Use our machine learning engine for predicting the expected waste amounts and types to always be prepared for tomorrow.
A client management system that saves time.
Manage waste producer and receiver documentation, waste amounts and types and possible pick-up requests. A fully integrated traceability system allows to automatically incorporate all client requests. Set up rules to automatically solve customer requests.
Effortless collaboration.
Was a container bin not placed outside in time, are you stuck in traffic, or is there another problem? Communicate it easily through the application to the administration, other drivers or waste producers.
All information a click away.
Make a note of the relevant pickup information at each address. Note what type of waste was collected, make photo’s, and scan the containers in case these are sensor-equipped. All data is immediately transferred to our algorithms for analysis.
Predict
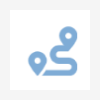
- Machine learning engine for predicting the expected waste streams.
- Historical analysis of the driven routes, made requests and collected waste.
- Fast data-driven insights to optimize fleet use through the map-based process monito
Optimize
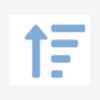
- Optimal for all vehicles, waste types and container types.
- Various optimization options: clusters, minimize travel time, minimize used vehicles.
- Dynamically adapt routes during the day.
Manage
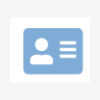
- Process monitor: follow the real-time progress during the day.
- Resolve client and driver requests manually or automatically.
- Full customer management solution and invoicing.
Flexible optimization
Our optimization algorithms help you find the best ways of collecting the waste streams. No matter how complex your processes, you have tens or thousands of locations to visit - our algorithm ensures you always have the optimal route.
Incorporate all restrictions.
We maintain a detailed and dynamic map, of the city which incorporates all waste collection restrictions based on waste types and vehicles permissions with time estimates obtained from our collection mobile app for a data-driven and flexible optimization
The classics and the state-of-the-art
Our algorithms are based on a combination of classical mixed-integer linear programming solvers and machine learning algorithms for finding the optimal schedules and routes.
An easy-to-use and navigation-friendly fleet management and tracking application
Our web and mobile applications enable you to track vehicles at any time and get notified of their exact locations. You can track their route, speed and direction on an interactive map; get informed with reports about the progress of your routes. Be notified of any delays and deviances in the road network and receive instructions on how to deal with them optimally and in a timely manner.
Benefit from the application of Geospatial Decision Software
Cyclefi’ reverse logistic application is an innovative decision-making digital tool with visualised mapping and the use of multiple levels of information for each spatial point. Design & generate maps with thematic units and make strategic decisions about next steps. Use databases of demographics, points of interest, and anything else that interests you.
Digital mapping of action points
Determine the effectiveness of your current waste collection service network and discover any service gap. Utilise data analytics to leverage existing opportunities to optimize your services.
The Future of Reverse Logistics
Track the progress of completed tasks
- The Proof of Collection (POC) feature refers to the system’s update on a task’s completion from the daily list. With just the touch of a button, you can comment, take a photo or get the recipient’s signature. The management center is informed accordingly and can intervene and modify the route or notify the customer. The daily delivery report is archived and used for strategic planning and evaluation.
Flexible Management
- Assign tasks by vehicle and driver and share the list with everyone involved.
- Set time windows depending on your staff’s working hours or your client’s availability hours.
- Specify the number and type of vehicles for each case, in which you transport perishable products with cold chambers, or under specific temperature conditions.
- Get optimal routing instructions and road traffic information to avoid delays.
Keep your customers notified on the delivery or visit
- Assign tasks by vehicle and driver and share the list with everyone involved.
- Set time windows depending on your staff’s working hours or your client’s availability hours.
- Specify the number and type of vehicles for each case, in which you transport perishable products with cold chambers, or under specific temperature conditions.
- Get optimal routing instructions and road traffic information to avoid delays.
Turn on special alarms
- Assign tasks by vehicle and driver and share the list with everyone involved.
- Set time windows depending on your staff’s working hours or your client’s availability hours.
- Specify the number and type of vehicles for each case, in which you transport perishable products with cold chambers, or under specific temperature conditions.
- Get optimal routing instructions and road traffic information to avoid delays.
Road traffic and precipitation
- Assign tasks by vehicle and driver and share the list with everyone involved.
- Set time windows depending on your staff’s working hours or your client’s availability hours.
- Specify the number and type of vehicles for each case, in which you transport perishable products with cold chambers, or under specific temperature conditions.
- Get optimal routing instructions and road traffic information to avoid delays.
Statistical Reports
- Assign tasks by vehicle and driver and share the list with everyone involved.
- Set time windows depending on your staff’s working hours or your client’s availability hours.
- Specify the number and type of vehicles for each case, in which you transport perishable products with cold chambers, or under specific temperature conditions.
- Get optimal routing instructions and road traffic information to avoid delays.